Based on the key concepts in topic 7.0, a new SIMPLIS Multi-Level MOSFET Driver was
developed for version 8.0. This model has several improvements over the driver model
developed in topic 7.0, but the core concepts have been preserved. In this topic, you will
create a test bench for this Multi-Level MOSFET driver using an XY Probe that is new in
version 8.0. Once you have characterized the behavior of this MOSFET driver, you will focus
on how to use it to estimate the switching losses of the main power switch, as well as the
overall efficiency, of a buck converter.
To download the example schematics for Module 7, click Module_7_Examples.zip
Key Concepts
This topic addresses the following key concepts:
- In order to obtain accurate estimates of switching losses, a good driver model is
equally as important as having a good MOSFET model.
- A simple test bench makes it easy to characterize a MOSFET driver. The test bench is
helpful in understanding the interplay between the driver and the power MOSFET during
switching transitions.
- When measuring power supply efficiency, good simulation technique is critical as
well as a good model.
- To obtain accurate results, the power supply system must be in a steady
state.
- There is a strong correlation between the number of "forced" data points per
switching cycle and the accuracy of efficiency and loss measurements.
What You Will Learn
In this topic, you will learn the following:
- How to use a simple test bench to characterize the output of a MOSFET driver .
- How different model levels of the Multi-Level MOSFET driver interact with Level 0
and Level 2 MOSFET models.
- How to use the efficiency calculator to estimate converter efficiency and the
switching losses of power MOSFETs.
- Two critical simulation techniques necessary for obtaining accurate loss and
efficiency estimates.
Background
The Multi-Level MOSFET driver was created to satisfy the driver model requirements
discussed in topic 7.0. For convenience, those requirements are repeated here. The
Multi-Level MOSFET driver allows you to do the following:
- Model the losses of a single MOSFET/driver combination including both conduction and
switching losses.
- Parameterize the MOSFET driver model so that it may be used as a general purpose
modeling block.
- Isolate the PWM driver input signal from the gate drive source and sink
currents.
- Provide a parameterized asynchronous delay to the PWM input signal, allowing
different values for the driver turn-ON delay and turn-OFF delay under no-load
conditions.
In order to characterize the behavior of this driver, you will examine its operation
under two different load conditions. To do this, you will create two test benches.
- First, a test bench that characterizes the Multi-Level MOSFET driver using a pure
capacitive load..
- Second, a test bench that characterizes this driver while driving an N-channel
MOSFET extracted to a level 0 model.
- Third, a test bench using a level 2 N-channel MOSFET.
Create Driver Test Benches
Since the ultimate objective is the evaluation of MOSFET switching losses with the
Multi-Level MOSFET driver model, at least two test-bench circuits are needed. The first
tests the driver model itself. To do this, we characterize Levels 0 and 1 of the
Multi-Level MOSFET Driver using a pure capacitive load. The second is to test the Driver
model while driving both Level 0 and Level 2 MOSFET models.
Test Bench #1
In the first test bench, you will test the driver
modeling block with a pure capacitive load. To get started, open
7.41_multilevel_driver_test bench_cap_load.sxsch, which is shown below.
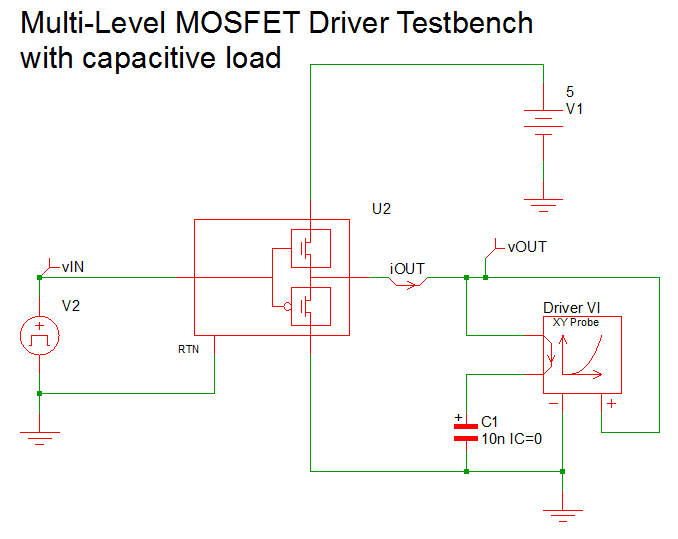
After opening the schematic, follow these steps
to the model level parameters:
- Set the Level 0 parameters as shown below.
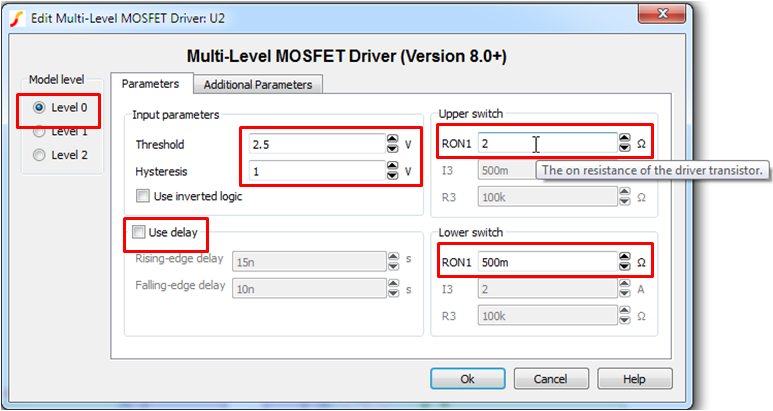
Note: the symbol is different depending on what model level is selected
and whether or not the user is modeling delay. In this exercise, you will not
use modeling delay.
- For Level 1, set the parameter values as shown below.
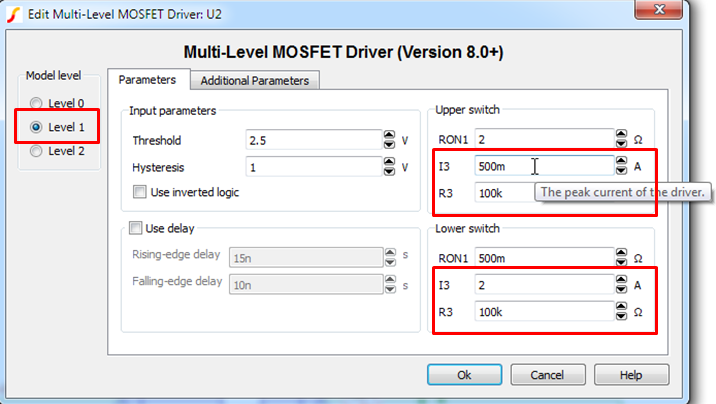
- Even though you will not explore the behavior of model level, for completeness,
set the following the parameter values for Level 2.
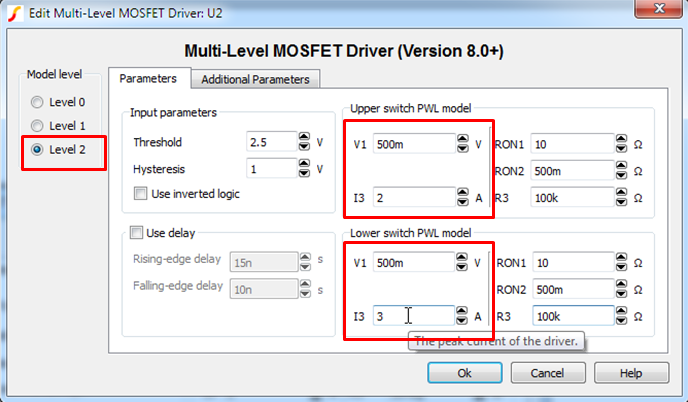
Model Level 0
Simulation
A detailed description of the Multi-Level MOSFET driver is
available by clicking on the Help button in the edit dialog for this part. The
Level 0 model is shown below.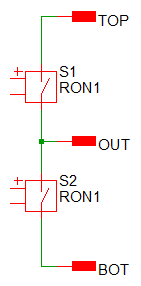
To run the Level 0 simulation,
follow these steps:
- In the Model level section, select Level 0.
- Press F9.
Result: After the simulation finishes,
the graph window opens with the results noted below.
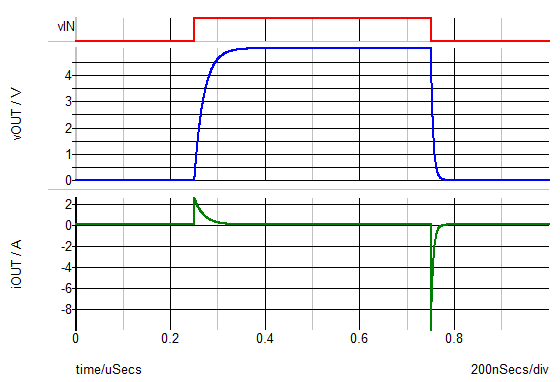
- When the capacitor voltage is initially rising, it is being charged
by a current equal to the supply voltage across RON1 of the upper
switch.
- The initial value of iOUT when the load capacitor is being charged is
5V / 2 Ohms = 2.5 A.
- The charging current iOUT then follows an exponential RC decay. As
the capacitor becomes fully charged, iOUT approaches zero.
- The discharge current behaves in an analogous fashion with its peak
current equal to -5V / 0.5 Ohms = -10 A.
Viewing the iOUT and vOUT waveforms plotted in
the iOUT vs. vOUT plane makes it easy to verify the key drive model break points
from the graph below. You can also determine the values of RON1 for both the upper
and lower switches from the slopes of the load lines during the charge and
discharge intervals of the capacitor voltage vOUT.
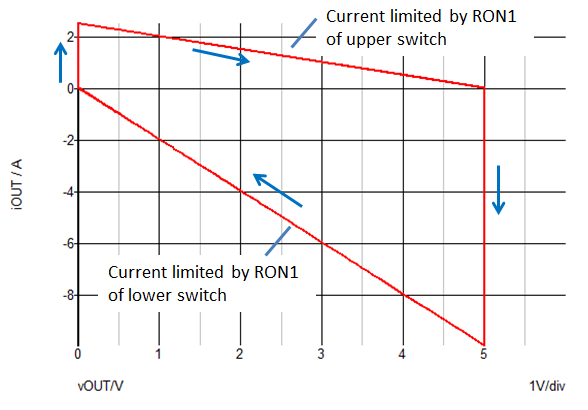
Model Level 1 Simulation
A detailed
description of the Multi-Level MOSFET Driver is available by clicking on the Help
button of the edit dialog for this part. The Level 1 model is shown
below.

To run the level 1 simulation, follow these
steps:
- In the Model level section, select Level 1.
- Press F9.
Result: After the simulation finishes,
the graph window opens with the results noted below.
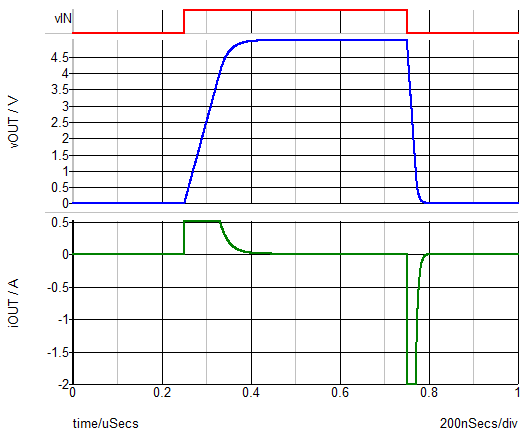
- With the Level 1 model of the Multi-Level MOSFET Driver, the maximum
charging current is limited by I3 of the upper and lower switches Q1
and Q2.
- In this case the maximum charging current is 0.5 A and the maximum
discharge current is -2 A.
From the iOUT vs. vOUT plot below, you can see
that the load capacitor is charged with a constant current I3 by the upper switch
until the voltage across the upper switch reaches a value of I3 * RON1, or (0.5 A
* 2 Ohms) = 1 V. Beyond this point, the charging current follows an exponential
decay determined by RON1 and the load capacitance. Similarly, during the discharge
interval, the load capacitor is discharged by a constant current of I3 = -2 A of
the lower switch until the voltage across the lower switch equals (2 A * 0.5 Ohms)
= 1 V before beginning an exponential decay.
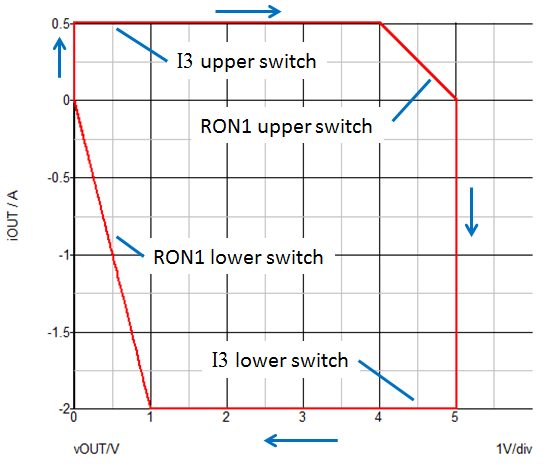
Test Bench #2
The next
test bench looks at the performance of the combination of the Multi-Level MOSFET
driver model and a Level 0 NMOS device driving a resistive load is shown below.
Important: Remember that with a Level 0 MOSFET model, you model the ON and
OFF resistance of a MOSFET with instantaneous switching between these two states. The
gate resistance and gate capacitance are also modeled.
To launch this simulation, follow these steps:
- Open the 7.42_multilevel_driver_test
bench_Lev0_mos_load.sxsch schematic.
- Verify that the Multi-Level MOSFET driver is set to Level 1.
- Verify that the Si4410DY MOSFET is set to Level 0.
- To run the simulation, press F9.
Result: The
steady-state waveforms generated by this schematic show the instantaneous
switching as well as the same charging and discharging behavior of the gate
capacitance that you observed in the test bench with the pure capacitive load.
The only slight difference is that at the initiation of turn ON and turn OFF,
there is an instantaneous step due to the 1.55 Ohm gate resistance of the
Si4410DY MOSFET.
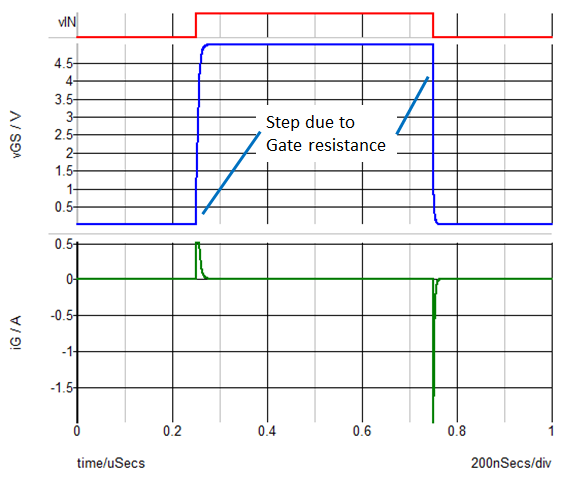
The effect of the MOSFET gate resistance is much more visible when you look at
these same waveforms plotted in iG vs. vGS plane. During both the turn-ON and
turn-OFF transitions, you see that the trajectory in the iG vs. vGS plane is
dramatically altered by the gate resistance. Again, it is much easier to determine
the critical modeling break points with this plot than it is with the time waveforms.
In fact, even if you did not know the gate resistance initially, it is easy to
measure gate resistance based on the slope of the trajectory in the iG vs. vGS plane.
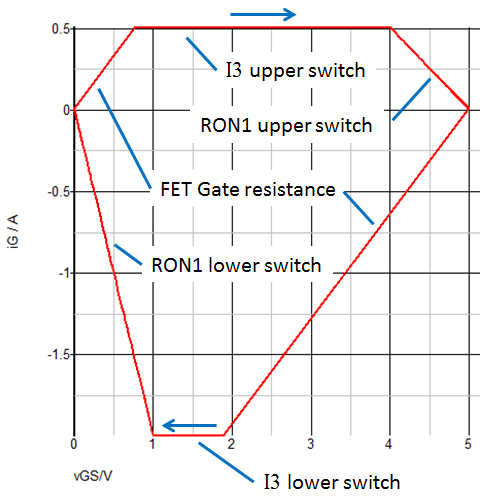
To find the smallest time constant, choose Simulator from the menu bar
and then select Show Smallest Time Constant so that you can use this as a
reference point in other test benches.
Result: You
should get the same result as displayed in the text on the schematic.
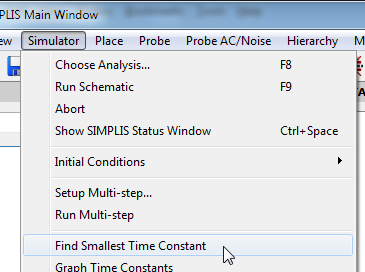
Test Bench #3
This test
bench uses the same resistive load as before but the MOSFET model is a Level 2
instead of a Level 0 as shown below.

To run this simulation, follow these
steps:
- Open 7.43_multilevel_driver_test
bench_Lev2_mos_load.sxsch.
- Verify that the Multi-Level MOSFET driver block is set to Level = 1 and that the
MOSFET Q1 is set to Level 2.
- Press F9.
Result: The resulting waveforms show the
expected Miller effect during turn ON and turn OFF. Note that the number of new
topologies increases significantly when you go from a Level 0 MOSFET model to a
Level 2. You also can see that the minimum time constant in base 10 is three
orders of magnitude smaller with the Level 2 model.
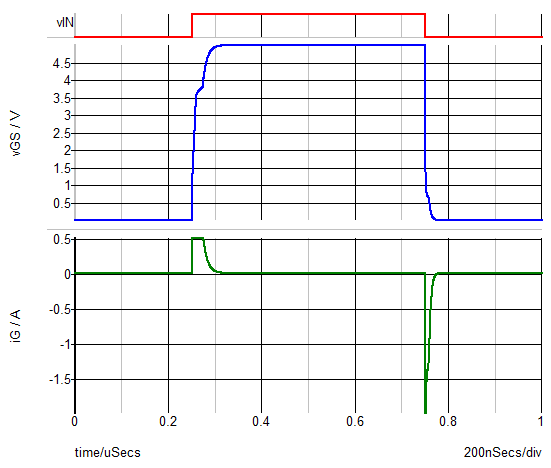
Although with the Level 2 MOSFET model, you can clearly see the Miller effect in
the time waveforms of iG and vGS, the trajectory in the iG vs. vGS plane is exactly
the same as with the Level 0 MOSFET model. Can you explain why this is so?
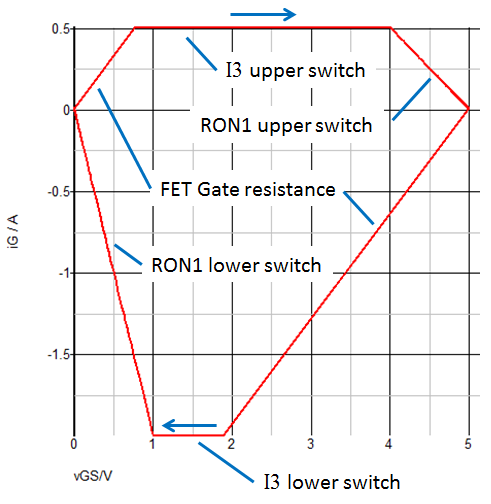
In order to obtain accurate estimates of switching losses, having a good
driver model is equally as important as having a good MOSFET model. You need a simple
test bench with a pure capacitive load to characterize the SIMPLIS Multi-Level MOSFET
driver. This same approach can be used to characterize a hardware driver even if the
published datasheet information is incomplete. Looking at the gate current and gate
voltage waveforms in the iG vs. vGS plane reveals the critical break points needed to
determine the appropriate Multi-Level driver model parameters.
Using the test benches presented in the topic, you can see how the current charging
and discharging the gate of a power MOSFET is determined primarily by current
limitations of the driver as well as by the gate resistance of the power FET. You can
also can appreciate how a good test bench is helpful in understanding the interplay
between the driver and the power MOSFET during switching transitions.
Before measuring switching losses and converter efficiency, follow these steps to
perform a quick experiment.
- Using the current test bench of 7.43_multilevel_driver_test
bench_Lev2_mos_load.sxsch, close any open waveform viewer results by
clicking Close all from the Waveform menu.
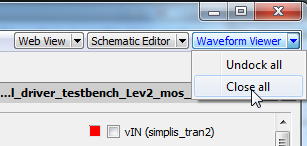
- Verify that the power MOSFET is set to Level 2.
- Verify that the driver is set to Level 1.
- To run the simulation, press F9.
- Without deleting any waveform results, change the driver level to level 0;
and then press F9 to run a second simulation.
Result: In the time domain results, look at vGS and iG, during the turn-ON transition
and you can see a noticeable difference in these waveforms. With the Level 0
settings, more current is available to charge the gate during the turn-ON
transition. This should not be surprising given the parameter settings used for
the Multi-Level MOSFET driver.
- Now look at the iG vs. vGS plot.
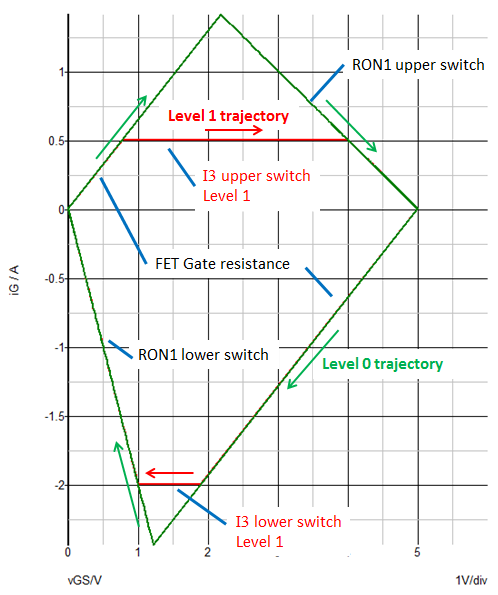
Note: The signature of the Level 0 driver trajectory is
different than that of the Level 1 driver trajectory in the iG vs. vGS plane.
This way of picturing the circuit operation can be helpful in developing a
fuller understanding of the complex behavior of a driver and MOSFET combination
during the turn-ON and turn-OFF transitions of a power switch. This depth of
understanding is important if you are to obtain accurate results when seeking
to simulate switching losses and converter efficiency.
In the next two sections, you will examine the simulation techniques that are essential
to obtaining accurate estimates of switching losses and power supply efficiency.
Simulate Switching Losses
A good vehicle to address the topic of simulating
switching losses and converter efficiency is the buck converter developed in the SIMPLIS
Tutorial (7.46_SIMPLIS_tutorial_buck_converter.sxsch).
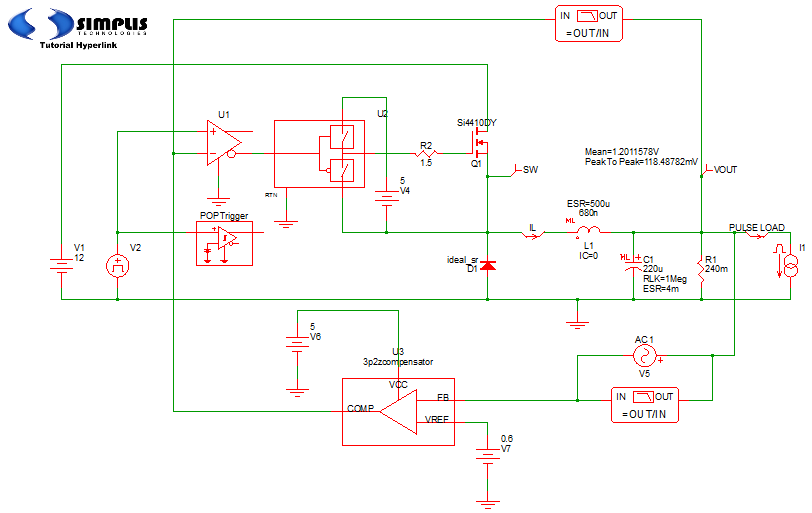
To modify this schematic in order to add
appropriate probes for loss measurements and to improve the accuracy of the loss models
of certain critical components, follow these steps.
- Add probes to measure the gate current iG and the gate-to-source voltage vGS as
shown in the highlighted oval near Q1 in the figure below.
Result: When you do this, you eliminate the resistor R2 that was in
series with the gate pin of Q1 in the original Tutorial schematic
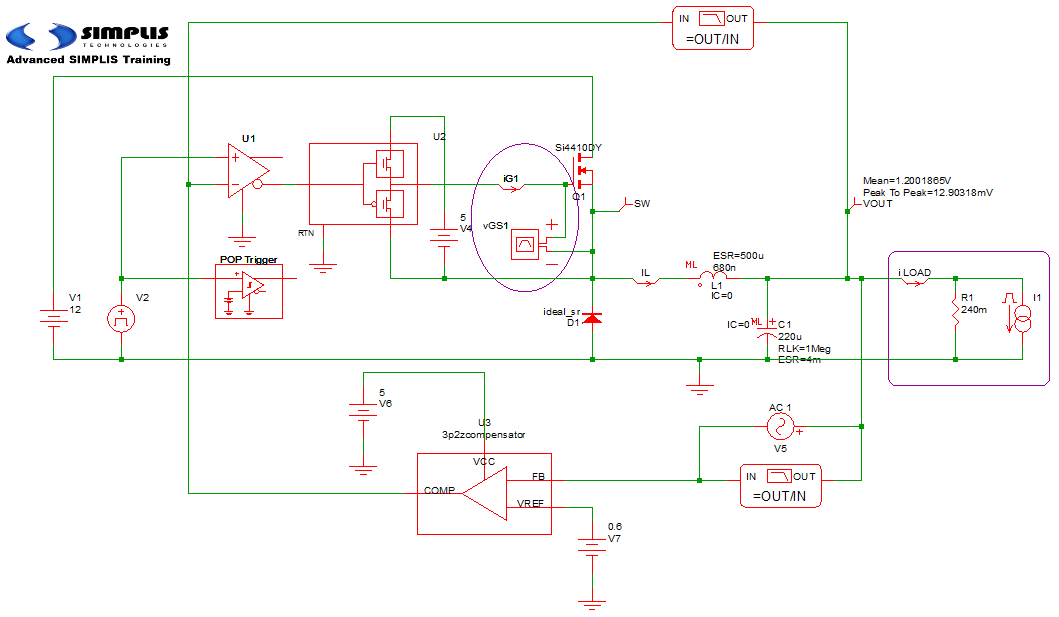
- To make it easier to measure the total load current, rearrange the relative
positions of the in-line current probe iLOAD and the load resistor R1 and load
current source I1 as indicated in the highlighted rectangle at the far right in the
illustration above.
- Make sure that the power MOSFET Q1 is set to Level 22.
Note: In order to accurately
model switching losses, it is essential to use a model level that accurately
simulates the switching transitions.
- Verify that the other MOSFET parameters are set to the values shown here.
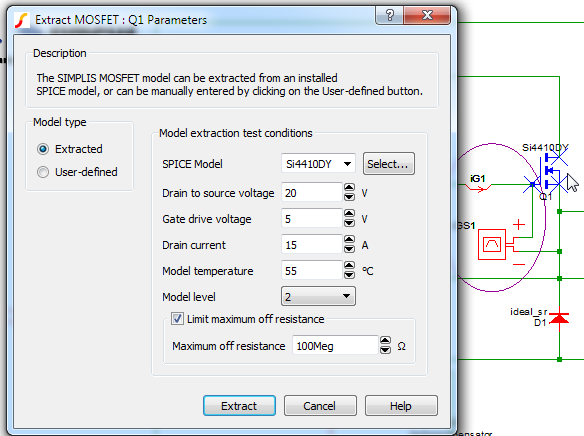
- To make sure the driver model can accurately simulate the driver transitions, verify
that the driver is set to Level 1 and that the other parameters agree with those
shown below.
Time Domain Waveforms
In this section you will verify that the time domain waveforms do, in fact, model the
switching transitions of the power switch Q1.
As will become clear in this discussion, accurate loss and efficiency measurements
require that the converter system be in steady state. You will also see that it takes a
surprising number of data points per switching cycle to obtain sufficient resolution of
the high frequency switching waveforms to yield accurate loss measurements. In all of
the following simulations, you will simulate exactly one cycle of steady state
operation. This allows you then to get the maximum benefit of each data point
that is calculated and output from a simulation.
Fow the next simulation, follow these steps:
- Open the schematic, 7.47_SIMPLIS_tutorial_buck_converter_mods.sxsch.
- From the menu bar, select , and then go ti the Periodic Operating Point (POP) tab.
- Click the settings button.
- Verify that the Number of cycles output is set to 1.
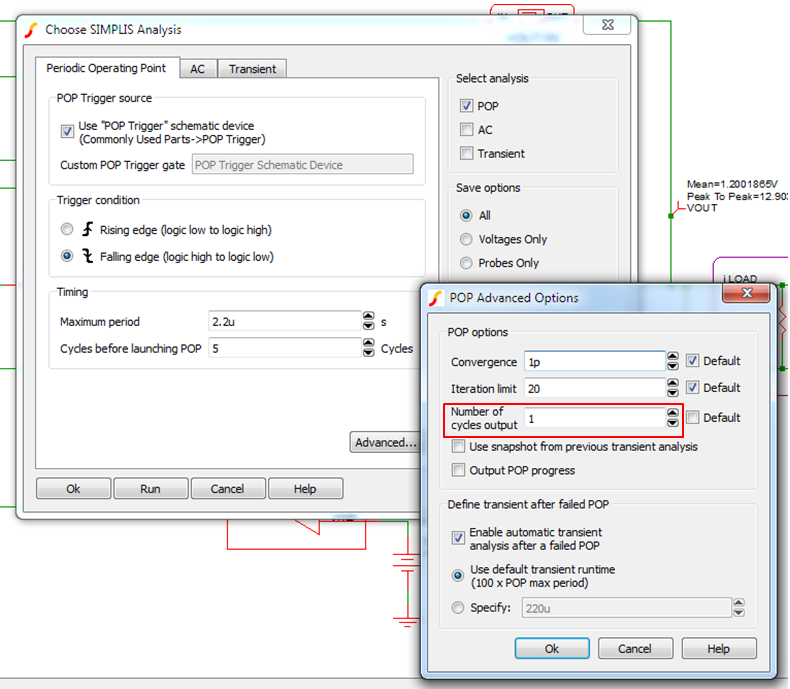
- Go to the Transient tab and set the Number of plot points to
5k.
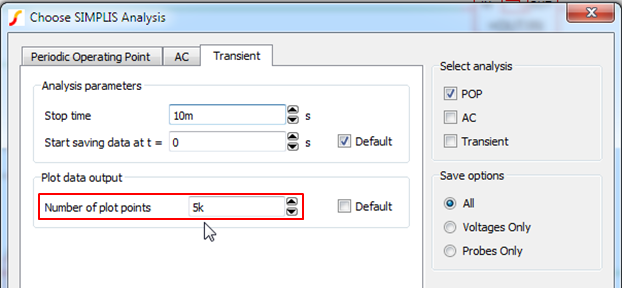
Result: This combination of POP and Transient
analysis settings will result in the simulation of one steady-state conversion
cycle and SIMPLIS will output a minimum of 5000 equally spaced data points.
Note: When the simulation objective is to measure various closed-loop
performance attributes of a switching power supply, such as a step-load transient,
the required number of data points per cycle is modest. Indeed, 5000 data points
per conversion cycle would be excessive in the extreme. However, when trying to
measure switching losses that occur during the turn-ON and turn-OFF transitions of
the power switch, as shown below, using 5000 data points per switching cycle will
typically reduce the numerical sampling error of a switching device loss
measurement to less than 0.5%.
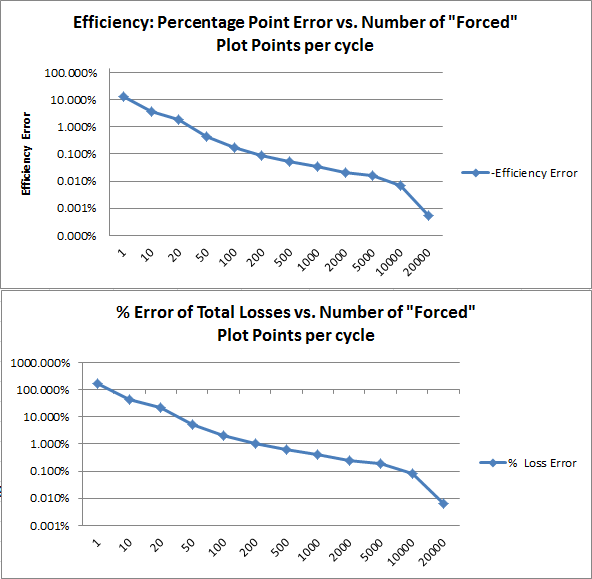
- Run a POP analysis of this circuit.
Result: Below are
the resulting steady-state waveforms of the gate voltage vGS1, gate current iG1,
switch node voltage SW and the inductor current iL.
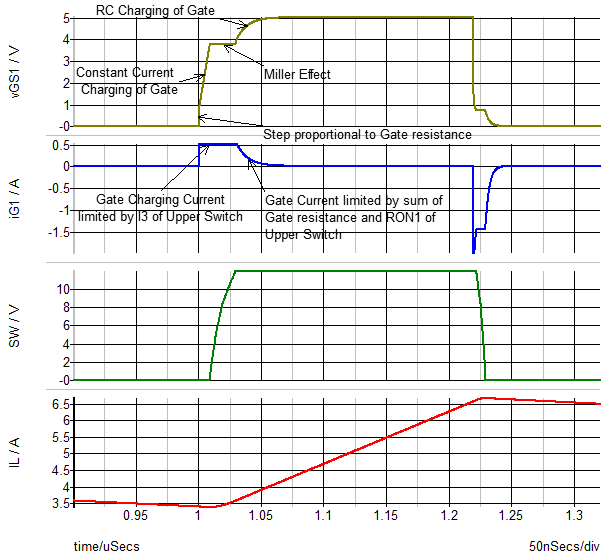
Observe the following results:
- During the turn ON transition, the gate current steps up to a value of I3 of the
upper switch in the Multi-Level driver model causing a small step in the gate voltage
that corresponds to the resulting voltage across the gate resistance of Q1, which in
this example is 1.55 Ohms.
- the gate voltage reflects the fact that the input capacitance of Q1 is charged by a
constant gate current equal to I3 until the gate voltage reaches a value that allows
all the inductor current iL to flow through Q1. At this point, the drain-to-source
voltage of Q1 begins its transition from high to low and the switch node SW
transitions from low to high.
- During the turn ON switching transition, assuming the gain of Q1 is reasonably high,
the gate voltage plateaus at a voltage such that the rate of change of drain-to-gate
voltage is equal to gate charging current divided by the nonlinear gate-to-drain
capacitance.
- Once the turn-ON switching transition is complete, then the gate voltage continues
to be charged up to its maximum value. This rate of charge is set by I3 until the
voltage difference between the driver positive supply node and the gate capacitor
decreases to the point where the charging current is then limited by the voltage drop
across RON1 of the upper switch + the gate resistance.
- The gate discharge and the resulting turn OFF transition happen in an analogous
fashion as shown below.
- There is one possible difference in the discharge waveforms. In this example, you
can see a second plateau in the gate current waveform iG1 during turn OFF that was
not present during the turn ON transition. This occurs because by the time that the
gate voltage reaches the voltage corresponding to the maximum inductor current iL,
the terminal voltage vGS is low enough that the discharging current is limited by the
series combination of gate resistance + RON1 of the lower switch in the driver
model.
Measure Power Supply
Efficiency
The final step in this topic is to demonstrate how to measure the
efficiency of a switching power supply, especially the losses associated with the power
switch Q1. The final schematic 7.48_SIMPLIS_buck_converter_measure_losses.sxsch shows
the result of employing the Efficiency Calculator to conveniently summarize all the
critical losses in the test bench circuit.
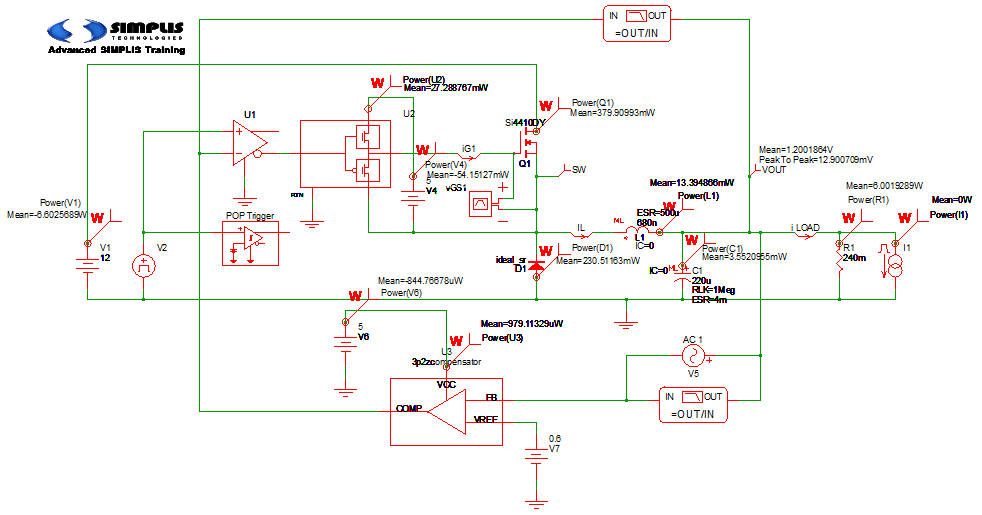
After adding the power probes to the schematic and defining the input sources
and output loads, a steady-state POP simulation is run. A Periodic Operating Point
analysis always results in steady-state time-domain waveforms that are an exact integral
number of steady-state switching cycles. This makes measuring the average powers
dissipated very straightforward.
To run the
efficiciency calculation, select from the menu bar.
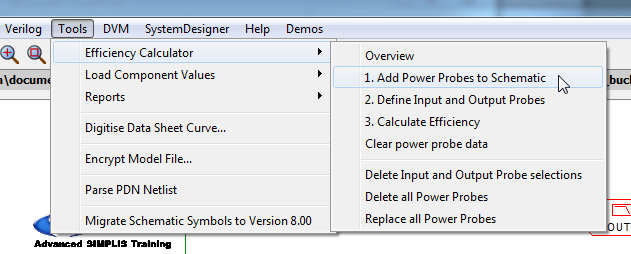
The results of the Efficiency Calculator are shown below. These results are
calculated based on the average power dissipated by each component with a power probe
attached to it. As is often the case, the largest contributor to the total losses is the
power lost in the main power switch Q1. Second is the loss in the rectifying diode
D1.
Discussion
The above discussion focuses on average
losses over a complete steady-state switching cycle. When optimizing the combined design
of a driver and a MOSFET, you need to look at the component portions of the switch
losses, turn ON, turn OFF and conduction losses. There are a number of ways to do this.
But one very easy one is shown here.
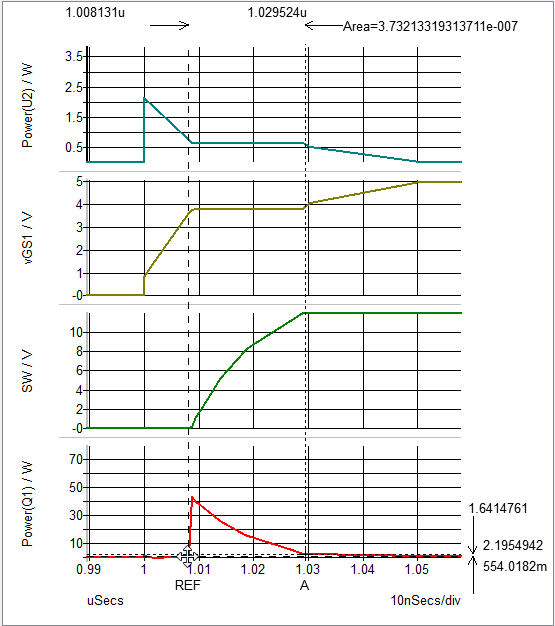
Notice that the calculated the area is under the instantaneous power dissipation
curve for Q1 during the turn ON transition. To accomplish this, set the cursors at the
beginning and the end of the turn ON transition, and then double click on the time
difference display. This action opens up a dialog window that allows us to request the
display of the area under the selected curve between the REF and A cursors.

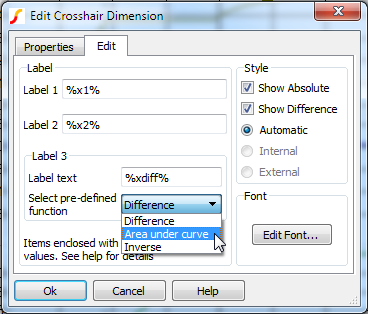
The result is that you have now calculated the energy dissipated in the MOSFET
during each turn ON transition. In this case, 0.37 uJ at 500 kHz results in a loss of
0.185 W.
Using the same approach to measure the turn OFF losses, you obtain 0.22uJ
of turn OFF energy, which results in a loss of 0.109 W. Using this approach, you
designer can scale the loss results by the switching frequency, which can be very
convenient when trying to optimize the overall design.
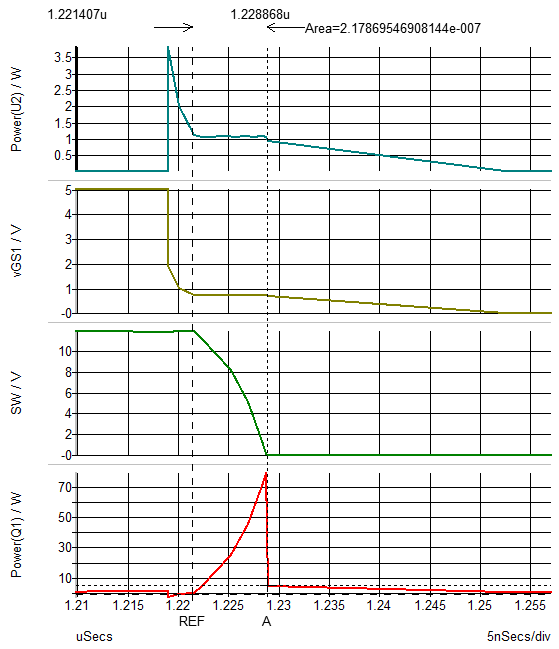
As is clear from the waveforms above, you would use the same approach to examine
the losses in the driver circuit.
This modeling approach provides a powerful
method for optimizing the design of a driver - power switch combination. The
parameterization of the driver allows you to independently control the turn ON and turn
OFF driver characteristics. The analysis approach allows you to optimize the driver
characteristics and the power MOSFET selection according to the application
requirements.
It cannot be emphasized strongly enough that for high efficiency
conversion systems, getting accurate estimates of overall efficiency requires that the
system be in a steady state. Output transients must be fully settled out in order to
obtain accurate results. Without a successful POP analysis, you must exercise patience
in running long transients to allow the system to reach that steady state. Especially as
circuits become more complex, the power of the POP analysis is stunning.
- First, the steady-state circuit solution is extremely accurate and is obtained
very quickly. Typically, POP runs much faster that a long transient. The POP
output is an integral number of cycles. This means that in order to find the
average power dissipation over an integral number of switching cycles, you can
average the instantaneous power dissipation waveform. There is no need to
carefully arrange cursors to average correctly.
- The other thing that POP accomplishes is that you dd not need to determine how
long a transient needs to be run in order to approach a reasonable steady-state
solution. Below is a plot of both the per-cycle converter efficiency and the
per-cycle efficiency error during a long transient simulation.
Since the switching period is 2 uS, this plots the efficiency for about
200 conversion cycles. This example circuit is not complex and is well designed
and well compensated; therefore, in this case and for this set of initial
conditions, you need to wait for only about 50 conversion cycles for the
efficiency error to be less than 0.1 percentage points. However, for more complex
circuits or worse initial conditions, the wait could be much longer. Also, extreme
care must be taken when running simulations that require so many data points. The
one simulation required to create these plots took up more than 10% of a laptop
hard drive.
-
An example showing how to plot out per-cycle efficiency and losses may be
found in the F11 window of the schematic 7.49_measure_per_cycle_losses_and_efficiency.sxsch.
Conclusions and Key Points to
Remember
- When using simulation to estimate switching losses in a switching power supply, a
good driver model is as important as having a good MOSFET model. For accurate
results, it is essential to model the current limitations of the driver.
- A simple test bench makes it easy to characterize a MOSFET driver. The test bench
is also helpful in understanding the interplay between the driver and the power
MOSFET during switching transitions.
- When measuring power supply efficiency, in addition to good models, good
simulation technique is critical.
- To obtain accurate results, the power supply system must be in a steady
state. As the system model becomes more complex, it becomes more and
more time consuming to use a long simulation to reach steady state.
Determining how long a transient is required to achieve a desired level of
accuracy is arduous and will help you appreciate the real power of the POP
analysis.
- There is a strong correlation between the number of "forced" data points
per switching cycle and the accuracy of efficiency and loss measurements. By
using only one thousand data points per cycle in this example, you were
introducing a data sampling error of about 0.4 percentage points of
efficiency. In other words, this data sampling error, in a 90% efficient
dc-dc converter was equivalent to 4% of the total losses in the system. To
reduce the sampling error below 1% of the total losses (or 0.1 percentage
points), you would have needed to use 10,000 data points per cycle.
- Long transients and thousands of data points per switching cycle are a
dangerous combination. It takes very little effort to fill up your hard
drive. Using the Periodic Operating Point analysis and outputting only one
cycle of data dramatically reduces this possibility.